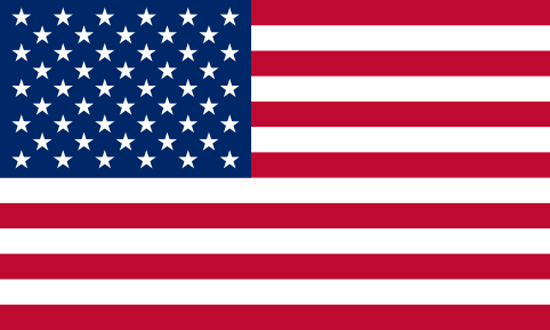
États-Unis
Numérotation des lots d'acier pour la production de casques
Production et laminage de l'acier
![]() Usine "South Work" de l'entreprise Carnegie-Illinois Steel Corporation située à Chicago dans l'Illinois. |
La "United States Steel Corporation" fut formée par JP. Morgan le 2 mars 1901 par rachat de la "Carnegie Steel Company", et fusion de la "Federal Steel Company" d'Elbert H. Gary et la "National Steel Company" de William Henry Moore pour la somme de 492 millions de dollars (équivalent à 15,12 milliards de dollars actuels) dont 226 millions de dollars pour Andrew Carnegie. |
Composante majeure de la corporation "US Steel", la firme "Carnegie-Illinois Steel Corporation" permit à cette dernière de se classer parmi les 16 plus grandes entreprises en termes de valeur de contrats de production au cours de la seconde guerre mondiale, devenant en 1943 le plus grand employeur avec 340 000 salariés.
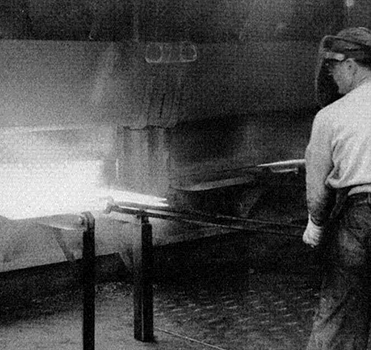
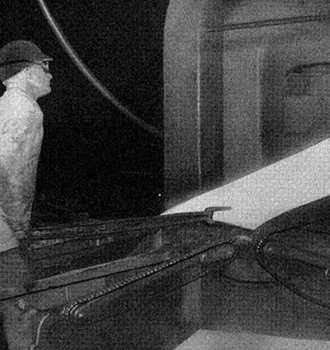
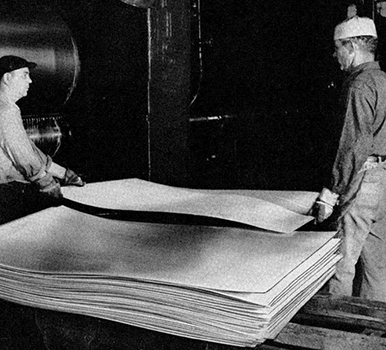
Étapes du laminage de l'acier chez Carnegie-Illinois Steel Corporation.
![]() |
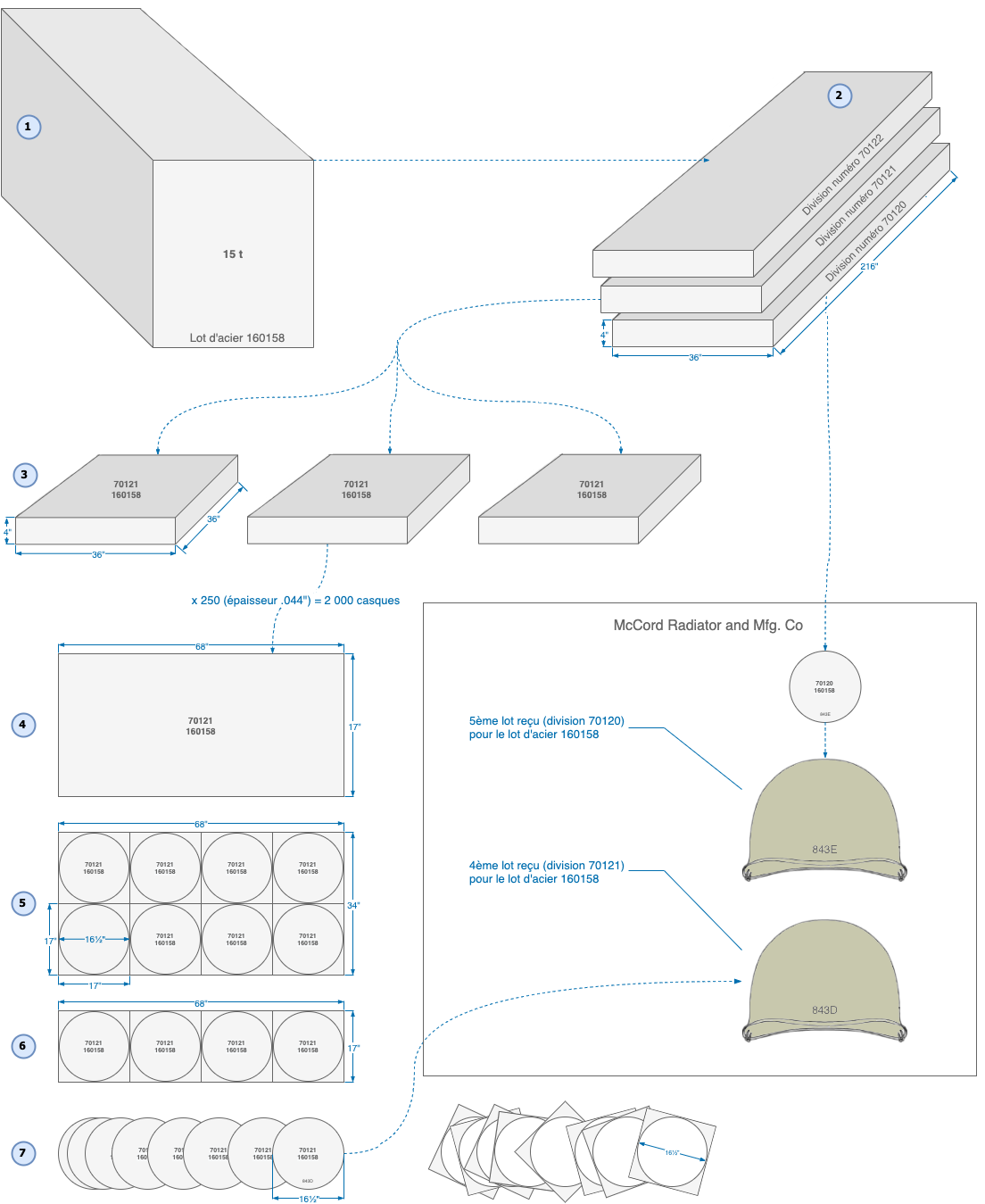
L'acier au manganèse fut produit dans l'usine de "South Work" située à Chicago dans l'Illinois, puis laminé dans l'usine "Gary Sheet Mill" située plus au Sud de la ville de Chicago dans l'état de l'Indiana :
- Les différents composants de l'acier au manganèse sont fondus dans un four à ciel ouvert à environ 1 500°C (2 800°F) puis coulés en un lingot de quinze tonnes. Un numéro de lot d'acier à six chiffres est affecté à chaque lingot permettant le suivi de toute la production (par exemple 160151).
- Afin de faciliter le suivi et le transport, chaque lingot de 15 tonnes est divisé en billettes (barre d'acier) qui sont laminées en plaque de dimension 216 x 36 x 4 pouces. Chaque division reçoit un second numéro de cinq chiffres pour assurer le suivi (par exemple : 70120, 70121, 70122… etc.). Ce numéro est systématiquement associé au numéro de lot et identifie la division d'un même lot d'acier.
- Chaque division est ensuite coupée en trois sections de dimension 36 x 72 x 4 pouces. Ces sections conservent la numérotation de la billette dont elles sont issues. Elles sont ensuite transportées dans l'usine "Gary Sheet Mill". Chacune des trois sections des billettes exempte de défaut peut produire 2 000 disques. Soit environ 6 000 disques pour une subdivision.
- Ces sections subissent plusieurs traitements, notamment le cisaillement, laminage, décapage et austénitisation (chauffe entre 800 et 900°C pendant un temps donné d'obtenir une structure cristallographique en austénite). Chaque section est ensuite laminée pour obtenir 250 plaques d'acier de dimension 68 x 34 pouces pour une épaisseur moyenne de 0,044 pouce. Chaque plaque conserve la numérotation de la section dont elle est issue.
- Les tôles d'acier austénitiques sont ensuite quadrillées en huit sections carrées de 17 pouces de côté. La numérotation de la subdivision du lot d'acier est tamponnée au centre de chaque section carrée.
- Ces tôles sont ensuite découpées sur l'axe longitudinale pour donner deux parties de quatre sections chacune.
- Chaque plaque est ensuite emboutie pour donner quatre disques de 16½ pouces de diamètre. Ces disques sont ensuite contrôlés, huilés et mis en paquet de 400 unités pour être transporté en train vers l'usine "McCord Radiator" de Détroit pour la fabrication de casques. Les rebus de l'emboutissage sont refondus lors de la coulée d'un nouveau lingot d'acier.
Production de casques chez "McCord Radiator and Mfg. Co"
![]() Locaux de McCord Radiator and Mfg. Co, situés à Détroit dans le Michigan. |
![]() |
![]() Fabrication de radiateurs pour automobile. |
L'usine "McCord Radiator manufacturing and co." située à Détroit dans l'état du Michigan est un manufacturier automobile. Elle est initialement connue pour la production de radiateur de refroidissement pour l'industrie automobile en plein essor aux États-Unis.
![]() Emboutissage. |
![]() Découpe. |
![]() |
![]() Mise en forme visière. |
![]() Production jonc. |
![]() Mise en place jonc. |
![]() Soudure du jonc. |
![]() Chaîne de mise en peinture. |
![]() Bout de chaîne, conditionnement. |
L'entreprise débute la production de casques en 1940 avec le déclenchement de la seconde guerre mondiale lorsque le "War Department" passa une commande par l'intermédiaire de l'arsenal de Rock Island pour la fabrication de 1 843 431 casques US 17 - A1.
Ce contrat ne fut pas totalement honoré en raison de l'adoption du casque M-1 par les forces armées américaines dont la production débute en juillet 1941. Le départ de la production du casque M-1 s'effectue à partir des disques d'acier initialement fabriqués pour le casque US 17 - A1.
L'entreprise "McCord Radiator" se fournira essentiellement auprès du producteur d'acier "Carnegie-Illinois Steel Corporation", et reçut à partir de 1943 une petite quantité de disques d'acier au manganèse de la firme "Sharon Steel Corporation" intervenant dans la production de casques M-1 à partir de 1943 lorsque la société "Schlueter Manufacturing compagny" obtint un contrat de production accordé par l'état américain pour soutenir la production de "McCord Radiator".
À chaque réception de caisses de disques au sein de l'usine "McCord Radiator", la numérotation appliquée sur chaque disque par la firme "Carnegie-Illinois Steel Corporation" est transposée sous une forme plus élémentaire de type alphanumérique pour assurer la traçabilité entre la production de l'acier et la fabrication de casques.
Le lot d'acier est identifié par un numéro incrémental partant de 1 (initié durant la production du casque US 17 - A1) et la subdivision est identifiée à l'aide d'une lettre sans forcément suivre l'incrément de numérotation de Carnegie mais est établie par ordre d'arrivée des lots. Le lettrage débute par A et s'incrémente en fonction du nombre de subdivision reçues par "McCord Radiator". À la fin de la seconde guerre mondiale, le lettrage sera particulièrement haut sous entendant des lots d'acier importants.
Cette numérotation permet d'assurer un contrôle de la qualité tout au long de la fabrication et d'identifier tous les casques produits pour un même lot d'acier : si un casque d'un lot et d'une subdivision présentait des défauts ou échouait aux différents tests prescrits (pliage, magnétique, microscopique et balistique), tous les casques issus de ce même lot pouvaient être identifiés puis vérifiés en vue d'une éventuellement élimination.
![]() Casque US 17 - A1. |
![]() Casque US M-1. |
![]() Casque US M-1. |
![]() Casque US M-3. |
![]() Casque USN Mark II. |
Malheureusement les registres ne fournissent que peu d'informations sur les dates de réception de l'acier et la fabrication de casques par "McCord Radiator". Seules quelques informations parcellaires sont parvenues jusqu'à nous : par exemple le lot 55A a été fabriqué aux alentours du 24 janvier 1942. Les lots 88 ont été produits le 8 avril 1942, les lots 148 le 24 juillet 1942, et les lots 863 et 865 ont été pressés le 19 août 1944.
Il n'existe aucune concordance archivée entre la numérotation établie par "Carnegie-Illinois Steel Corporation" et son équivalence alphanumérique de "McCord Radiator".
Une charte graphique a été établie permettant la datation approximative des casques M-1 produits entre juillet 1941 et août 1945 sur l'évolution des numéros de lot estampés sous la visière des casques produits par la société McCord.
Cette charte a été créée sur l'observation de nombreux casques M-1 en référençant leurs caractéristiques techniques, tout en sachant que certains éléments ont changés à des dates butoir (apparition des pontets mobiles, jointure du jonc arrière) ou d'autres éléments ayant débuté leur apparition à partir d'une certaine date sans forcément être une obligation (changement des éléments métalliques de la jugulaire). Aussi les quelques dates connues pour certains lots permettent de conforter cette charte.
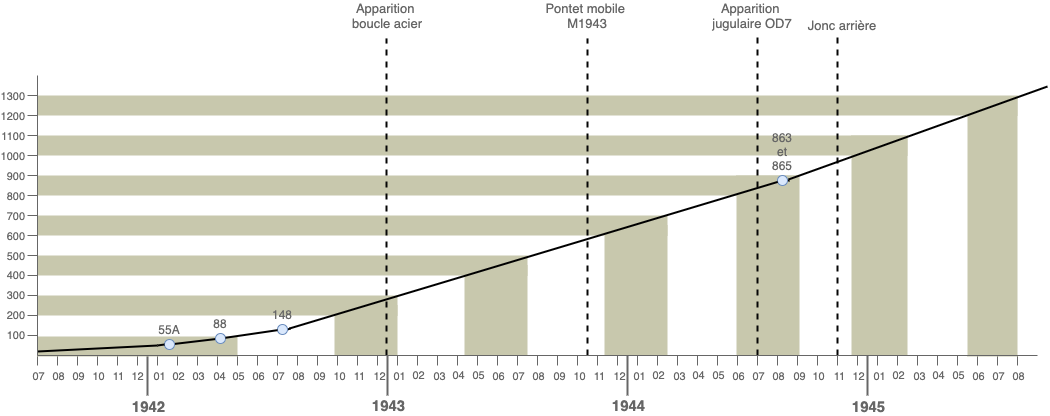
Cet outil permet donc de dater approximativement la date de réception du lot de disques associé à un lot d'acier produit par "Carnegie-Illinois Steel Corporation". Cette datation est d'autant plus aléatoire pour dater la production d'un casque associé à un numéro de lot en raison des aléas évidents d'une production industrielle :
- Il a clairement été établi que la production mensuelle n'est pas équivalente tout au long de la production comme en témoigne un document de planification et d'estimation de la production de casque M-1 pour l'année 1945. Il doit aussi en être de même pour la production d'acier côté "Carnegie-Illinois Steel Corporation".
![]() |
Estimation et planning de production de casques M-1 pour l'année 1945. |
- À production mensuelle inégale, il faut aussi prendre en compte que chaque mois ne compte pas le même nombre de jours.
- Les lots de disques ont-ils été mis en production dès réception ou ont-ils été stocké avant production ? Si stockage, combien de temps ? Pour une production mensuelle non égale avec une réception d'acier régulière, il est logique qu'il y ait eu un stockage des disques reçus avant mise en chaine de production.
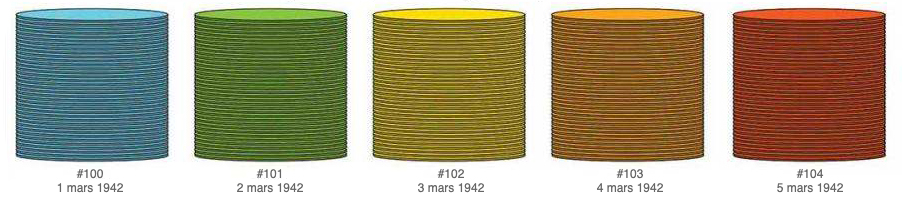
Modélisation d'une production parfaitement linéaire.
- Les lots de disques ont-ils été employés de manière parfaitement séquentielle jusqu'à épuisement avant de passer au suivant ? Pour une chaine de production conventionnelle, chaque ligne de production est approvisionnée de manière régulière. Ainsi, les disques de la veille non utilisés sont passés en dessous de la pile et peuvent être employés avec plusieurs jours de décalage.
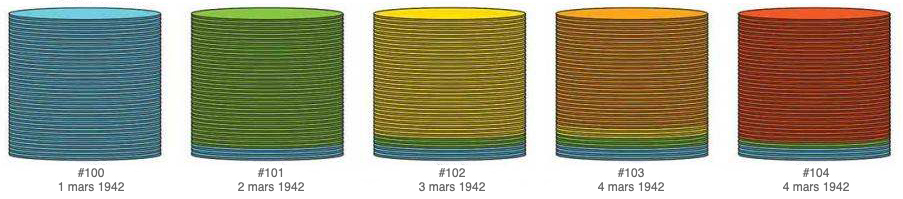
Modélisation d'une production parfaitement linéaire.
![]() |
Ne pas confondre numérotation à réception de l'acier et production des casques. En prenant compte de tous ces critères, il convient d'élargir la plage approximative de datation de la fabrication du casque pouvant être effectué avec un important décalage par rapport à l'incrément du numéro de lot d'acier qui est effectué lors de la réception des disques d'acier. Alors que ces marquages estampés à froid dans l'acier sont très lisible sur les casques US 17 – A1 car présent sur une zone non étirée lors de l'emboutissage du casque, ils le sont moins sur les casques M-1 où l'acier est étiré sur toute la surface du casque. En résulte une fâcheuse manie des collectionneurs de retirer la peinture sur cette zone afin de faire ressortir le marquage alors qu'un simple passage à la craie suffit. |
Production de casques M-1 chez "Schlueter Manufacturing Co"
![]() "Sharon Steel Corporation" basée à Farrell, en Pennsylvanie. |
![]() Locaux de "Schlueter Manufacturing Co", situés à Saint Louis dans le Missouri. |
Le second producteur d'acier à intervenir dans la production de casques M-1 est la firme "Sharon Steel Corporation" (ou "Sharon Steel Hoop Company" avant 1936) basée à Farrell, en Pennsylvanie. La "Sharon Steel Corporation" tire ses racines de la "Sharon Steel Hoop Company", fondée le 8 octobre 1900 par Morris Bachman. Cette création intervient au moment d'un boom de l'activité sidérurgique liée à l'exploitation de la houille sur les bords de la Shenango. |
![]() Plaquette publicitaire pour l'acier Sharon. |
![]() |
La société "Schlueter Mfg co." est initialement connue pour l'emboutissage de biens de consommation métallique, elle produira environ 10% de la production totale de casque M-1 durant la seconde guerre mondiale uniquement en acier "Sharon Steel".
"Schlueter Mfg co." reprit la même identification alphanumérique des lots d'acier "Sharon Steel" que l'usine "McCord Radiator" sous laquelle elle ajoute la lettre S afin de bien distinguer sa production, notamment une fois distribuée aux forces armées américaines.
De manière similaire à "McCord Radiator", il est possible d'éditer une charte graphique permettant de visualiser l'évolution de l'incrémentation de ces numéros de lot au cours de la production. Cette charte permet donc de dater de manière très approximative la production d'un casque par la firme "Schlueter Mfg co." tout en gardant en tête qu'il ne tient pas compte des aléas de production qui furent important chez ce fabricant.
![]() |
![]() |
![]() |
![]() |
![]() |
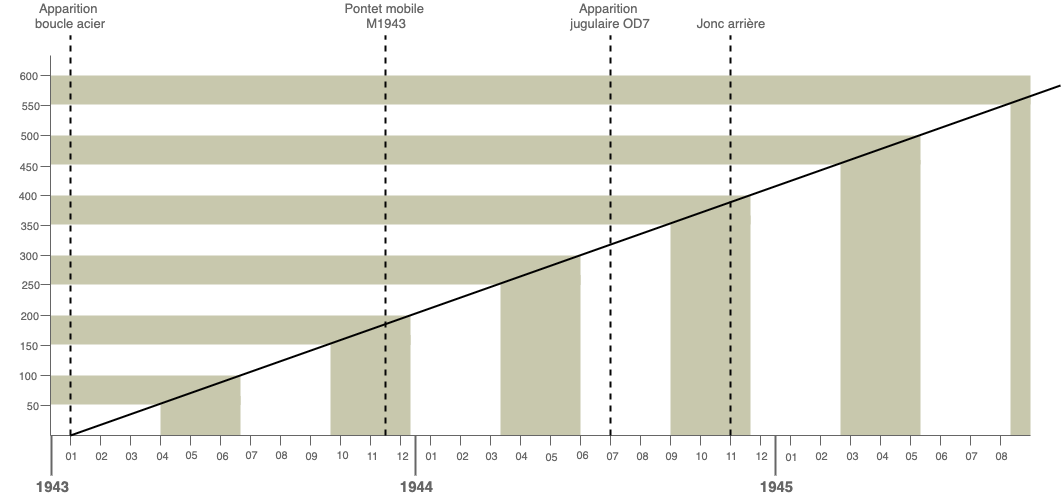
Production de casques M-1 chez "Parish Pressed Steel Company"
À la fin de l'année 1944, en raison de la fluctuation des exigences de production en constante augmentation et la pénurie de main d'œuvre dans les villes de Détroit et Saint Louis, il fut accordé un nouveau contrat de production de casques M-1 à la société "Parrish Pressed Steel Compagny" située à Reading dans l'état de Pennsylvanie pour augmenter la capacité de production de casques M-1. Un autre contrat fut accordé à la firme "Reading Hardware compagny" située dans la même localité pour les dernières étapes de production (mise en place du jonc, peinture et assemblage des jugulaires).
Ces contrats prévoyaient une production de 80 000 unités par mois avec un départ de production en avril 1945 pour une production totale de 460 000 casques. En raison de la fin des hostilités en septembre 1945, ce contrat ne fut pas honoré en intégralité et on ignore combien de casques furent produits en totalité.
![]() |
![]() |
Les casques M-1 emboutis par la société "Parrish Pressed Steel Compagny" présentent une forme caractéristique avec une visière particulièrement prononcée. |